Summary:The compression molding process of carbon fiber rectangular tube is to put a certain amount of prepreg into the cavity of the metal mold, use a hot press to generate a certain temperature and pressure, and make the carbon fiber under a certain temper......
The compression molding process of carbon fiber rectangular tube is to put a certain amount of prepreg into the cavity of the metal mold, use a hot press to generate a certain temperature and pressure, and make the carbon fiber under a certain temperature and pressure after closing the mold. Prepreg is a process method in which the prepreg is heated and softened in the mold cavity, flowed under pressure, filled with flow, filled with the mold cavity and solidified to obtain a product. The main steps are as follows.
①Preparation. Do a good job in the supporting work of prepreg, forming tooling and mold, and furnace test pieces;
②Prepreg cutting and layering. After the re-inspection of the prepreg is qualified, it shall be cut according to the material sample, and laid up according to the product lay-up requirements;
③Moulding. Load the stacked prepreg into the mold, and close the mold according to the process regulations for pre-compaction to make its structure compact;
④ Curing and forming. Carry out curing and molding according to the requirements of the process documents, and strictly control the parameters of each curing process.
⑤Demoulding and cleaning. Carry out demoulding and trimming according to the requirements of the process documents, and clean up the tooling mold;
⑥Test with the test piece in the furnace. Process the test piece with the furnace according to the requirements of the process document, and conduct the test according to the test method standard;
⑦Non-destructive testing and final inspection. Carry out non-destructive testing and final inspection of the products according to the requirements of the design documents.
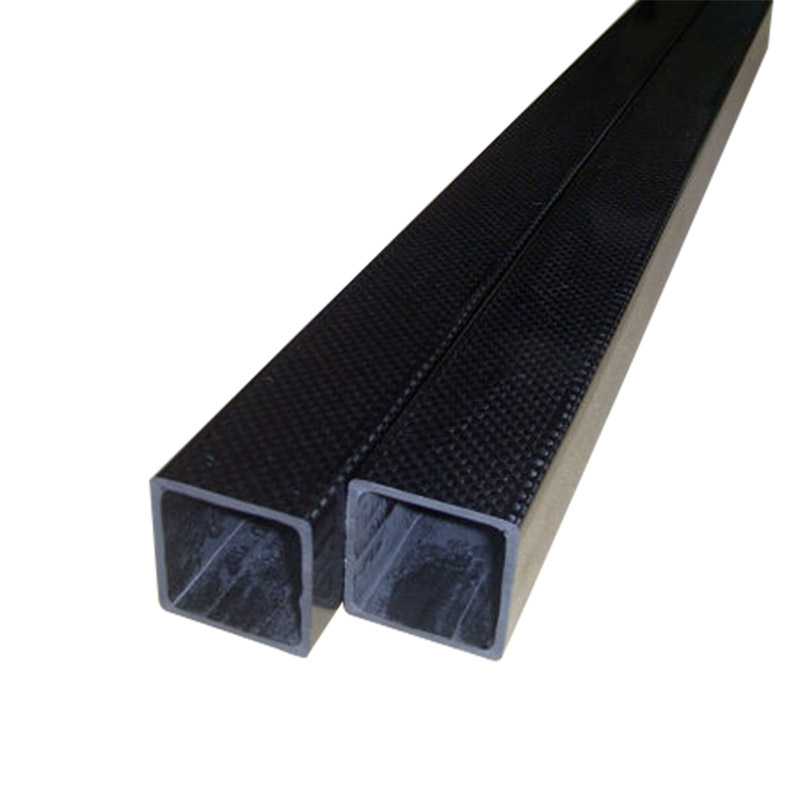
The characteristic of the compression molding process is that heating is required during the molding process. The purpose of heating is to soften and flow the resin in the prepreg, fill the mold cavity, and accelerate the curing reaction of the resin matrix material. When the prepreg fills the mold cavity, not only the resin matrix flows, but also the reinforcement material flows, and the resin matrix and reinforcement fibers fill all parts of the mold cavity at the same time. The resin matrix has a high viscosity and strong cohesive force, so it can flow together with the reinforcing fibers. Therefore, the molding pressure required for the molding process is relatively high, which requires the metal mold to have high strength, high precision and corrosion resistance, and requires a special The hot press is used to control the process parameters such as temperature, pressure, and holding time of curing and molding.
Unlike autoclave molding, compression molding of carbon fiber rectangular tubes does not require prepregs and tooling molds to be placed in the tank. It has good observability and a large range of pressure adjustment, the internal quality of the structure is easy to guarantee, and the accuracy of the external dimensions is high, so it is widely used in the manufacture of composite structural components with complex shapes. Such as composite engine blade compression molding.
The compression molding method has high production efficiency, accurate product size, and smooth surface. Especially for composite products with complex structures, it can generally be formed at one time without damaging the performance of composite products. Its main disadvantage is that the mold design and manufacture are relatively complicated, and the initial investment is relatively large. Nevertheless, the mold forming process method still occupies an important position in the composite material forming process.