Summary:Carbon fiber composite materials are typically difficult materials to process. Parts with complex shapes are usually made by material molding, but often require secondary processing after molding to meet accuracy and assembly requirements. Due to the......
Carbon fiber composite materials are typically difficult materials to process. Parts with complex shapes are usually made by material molding, but often require secondary processing after molding to meet accuracy and assembly requirements. Due to the material's high strength and hardness, low thermal conductivity, low anisotropy and low interlayer bond strength, conventional treatment methods cause processing defects such as delamination, cracks, burrs and fiber extraction. Often, it is difficult to achieve a high level. values. Because the processing precision of carbon fiber composite material is high, the tool wears heavily and the processing cost is high, it takes a lot of time and effort to process and process carbon fiber composite material. Although non-conventional treatment methods such as laser treatment, water jet treatment and ultrasonic treatment are used to treat carbon fiber composites, they often have large thermal impact zones, impact damage, brittle delamination, etc. Processing defects such as cracks occur. .
EDM is a heat treatment. The local and instantaneous high temperatures produced by the pulse spark discharge between the two poles destroy the treated material by melting, cooling or vaporizing. This is a common unconventional processing method. No direct processing method. Mechanical contact during processing It is suitable for processing conductive materials with high hardness, high strength and high brittleness, regardless of the mechanical properties of the material, and can achieve high processing accuracy. Widely used in aerospace, mold making etc. Industry.
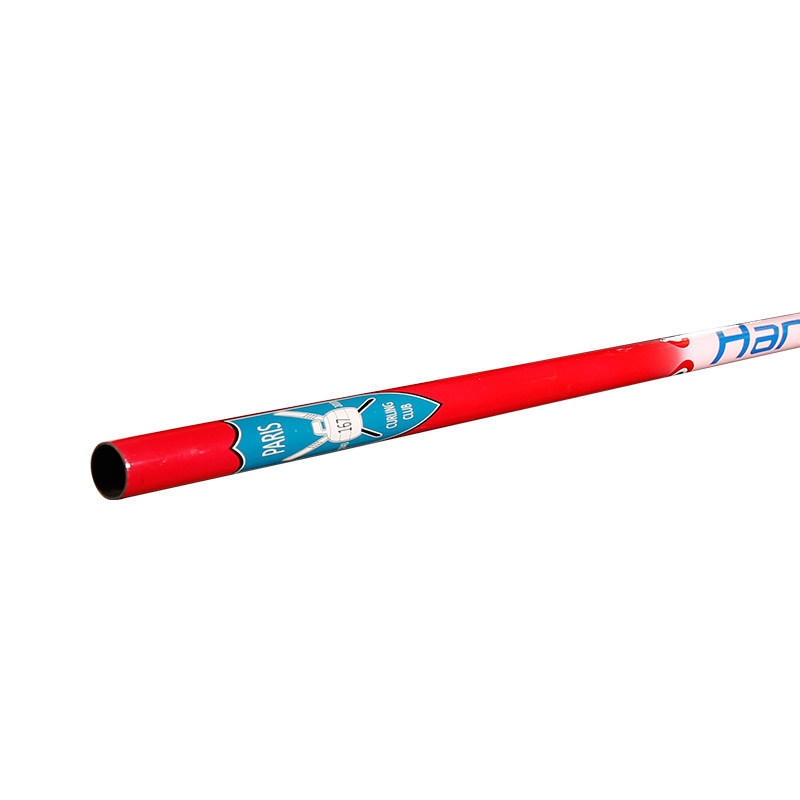
Wire EDM uses a moving metal wire as an electrode to perform discharge erosion, cutting and molding work. According to the linear speed of the electrode wire, it can be divided into high-speed wire and low-speed wire. Brass is typically used for low-speed wire processing. The wire and electrode wire move in one direction and the wire speed is usually 0.2 m/s or less. It can be cut many times and achieve high processing accuracy. It has clear advantages for precision machining of difficult materials, plates, specially shaped holes, narrow slits and complex shaped workpieces. It is important to use wire EDM in the field of carbon fiber composite material processing to facilitate the development of carbon fiber reinforced composite material processing and application fields and to eliminate the processing defects caused by conventional processing.
Studies have shown that large differences in thermal conductivity and melting point and boiling points of EDM CFRP, carbon fibers and epoxy resins provide a clear direction for material cutting. Studies show that bare carbon fibers often lead to short circuits. The pulses range from 10% to 60% of the total number of pulses, but CFRP EDM processing increases the CFRP cutting rate due to short circuit phenomena. On the machine surface, the short circuit phenomenon is likely to occur and the material removal rate is high. , the smaller the discharge gap, the less frequent the short circuit phenomenon. CFRP has anisotropy, the discharge pits in different directions have different shapes and the material erosion rates are different, resulting in non-uniform steps on the machined surface. When the feed direction is parallel to the fiber direction, the material removal rate is higher than in the vertical direction.
When observing the properties of EDMCFRP using a thermal camera, the shape of the discharge trajectory depends on the placement direction of the carbon fibers, not the current, and the discharge energy is consumed by the carbon fibers. surface of the workpiece. As the pulse power increases, defects such as delamination and heat infection zones increase, surface roughness increases, and higher processing quality can be obtained by processing at lower power. Introduce compressed air and deionized water to the top and bottom of the workpiece to form a special fixture to cool the surface of the hole inlet and outlet in time and blow out the arc and improve the processing quality. .. Compared with non-spray, spray processing can effectively reduce the heat on the inlet and outlet surfaces, improve the affected areas, improve the processing accuracy and surface quality, and improve the processing efficiency by about 21.6%.
Founded in 2006, Jiaxing Longshine Carbon Fiber Products Co., Ltd. is China Custom Carbon Fiber Composite Manufacturers and OEM Carbon Fiber Material Suppliers, located in the center of Yangtze River Delta, the state-level Xiuzhou High-tech Industrial Development Zone of Jiaxing. In recent years, we committed to the r&d and production of carbon fiber and other composite materials in the military and civil fields, including participating in the R&D and production of C919 aircraft parts, high-speed rail accessories, and several logistics support projects.Production process: autoclave, tube rolling, molding, bag pressing, extrusion, winding and vacuum diversion assisted molding process.Product type: tube/pipe, plate (solid/sandwich), 3D products.In recent years, we committed to the r&d and production of carbon fiber and other composite materials in the military and civil fields, including participating in the R&D and production of C919 aircraft parts, high-speed rail accessories, and several logistics support projects. OEM custom Carbon Fiber Composite & Material.We are willing to sincerely work with you, win-win cooperation, and strive to make the enterprise become the industry leading, customer satisfaction, harmonious team quality enterprise, contribute to the development of the whole industry and the needs of the country.