Summary:With the development of carbon fiber prepreg technology and the quality stability and reliability requirements of carbon fiber composite materials, the hot melt method has been widely used in my country's aviation systems. The process of preparing pr......
With the development of carbon fiber prepreg technology and the quality stability and reliability requirements of carbon fiber composite materials, the hot melt method has been widely used in my country's aviation systems. The process of preparing prepreg by hot melt method has higher requirements on carbon fiber than drum method. From the analysis of development requirements, in order to strictly control the quality of carbon fiber prepreg, the article puts forward the following main requirements for the process performance of domestic high-modulus carbon fiber:
1. No broken ends, as few filaments as possible. In the process of preparing carbon fiber prepreg, once the carbon fiber breaks, it is necessary to stop the wire connection, which will cause appearance quality problems in some areas. The process of preparing prepreg by hot melt method often uses dozens to hundreds of yarn spools. If there is a broken end, it will reduce production efficiency and waste materials, and will affect the quality of prepreg.
In the process of prepreg preparation, carbon fiber will pass through a series of guide shafts and rolling rollers, and there are many hairs, and after mechanical friction, it is easy to form hairballs, which makes the surface of the prepreg uneven and affects the uniformity of its thickness. Practical work has shown that the resin content will increase significantly at the prepreg ball, and it will also cause uneven distribution; once the ball is formed, it will result in more broken wires. In addition, if there are too many carbon fibers, it will pollute the production environment and bring harm to the health of prepreg operators.
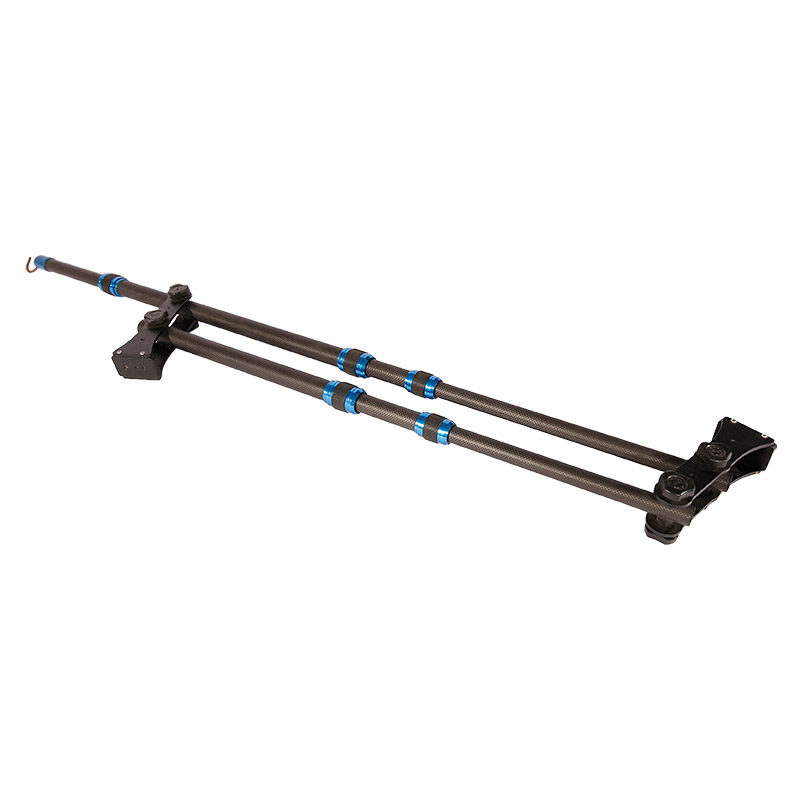
2. The linear density is stable and the discreteness is small. In order to correctly calculate the amount of carbon fiber per unit area when preparing carbon fiber prepreg, the linear density of carbon fiber must be controlled first. The good stability of carbon fiber quality of Japan Toray Company is mainly reflected in the control of the stability of its linear density. In the early 1980s, the offline coefficient index of the linear density of T300 and M40 was less than 3%. The measured value of the linear density dispersion coefficient of different batches of carbon fibers in the 1990s was less than 1%, which made the preparation of carbon fiber prepregs effective. Controlling the stability of carbon fiber dosage per unit area creates favorable conditions.
3. Reasonable sizing treatment In the carbon fiber manufacturing process, in order to improve its operational performance, The carbon fibers are pre-treated with sizing. Practice has shown that not one sizing agent is suitable for every carbon fiber, and not every sizing agent is compatible with every resin matrix. Therefore, carbon fiber manufacturers should have different types of sizing agents to adapt to different carbon fiber reinforced materials and resin matrix materials. In addition, the amount of sizing agent should be controlled to create favorable conditions for the quality control of carbon fiber expansion to prepare ultra-thin prepreg, carbon fiber and resin matrix wettability in the future.
4. Determine whether the carbon fiber has a twist or not. For carbon fiber fabric products, generally use twisted carbon fiber, so that in the weaving process, the fluff can be reduced and the product uniformity is good. In the preparation of carbon fiber thin-walled structural composite materials, in order to reduce the structural quality and facilitate the process layer design, untwisted carbon fibers must be used to fully widen the carbon fibers and prepare ultra-thin prepregs to meet product structural design requirements. Therefore, it should be proposed to the manufacturer to manufacture twisted or untwisted carbon fibers according to the different uses of carbon fibers.
5. Sufficient continuous length When the prepreg is prepared by the hot melt method, the continuous length of each tube of carbon fiber is different. As long as one tube of carbon fiber is used up first, the yarn must be stopped to ensure continuous production, but then the carbon fiber is used up one after another. , it is necessary to stop in sequence, which not only reduces the production efficiency, but also difficult to control the quality of the prepreg. Therefore, the length of each tube of carbon fiber is required to be controlled within a certain range, which is conducive to the quality assurance of prepreg preparation.
6. Better storage stability. Carbon fiber has to go through a series of processes such as quality inspection, production, storage, and transportation from the date of production to the production of composite structural parts. Some processes take a long time, so there must be a specified storage period. During this period, the carbon fiber should maintain its original state and process operability, such as weaving, winding, prepreg preparation and other processes of carbon fiber without damage and performance degradation.
Founded in 2006, Jiaxing Longshine Carbon Fiber Products Co., Ltd. is China Custom Carbon Fiber Composite Manufacturers and OEM Carbon Fiber Material Suppliers, located in the center of Yangtze River Delta, the state-level Xiuzhou High-tech Industrial Development Zone of Jiaxing. In recent years, we committed to the r&d and production of carbon fiber and other composite materials in the military and civil fields, including participating in the R&D and production of C919 aircraft parts, high-speed rail accessories, and several logistics support projects.Production process: autoclave, tube rolling, molding, bag pressing, extrusion, winding and vacuum diversion assisted molding process.Product type: tube/pipe, plate (solid/sandwich), 3D products.In recent years, we committed to the r&d and production of carbon fiber and other composite materials in the military and civil fields, including participating in the R&D and production of C919 aircraft parts, high-speed rail accessories, and several logistics support projects. OEM custom Carbon Fiber Composite & Material.We are willing to sincerely work with you, win-win cooperation, and strive to make the enterprise become the industry leading, customer satisfaction, harmonious team quality enterprise, contribute to the development of the whole industry and the needs of the country.